Discover how SeekOps combines its Ground Control Station with the FASTR system to stream real-time methane data, accelerate reporting, and give operators actionable insights during flight.
Read time: 5 minutes
Real-Time Awareness with GCS
When we fly a site, our UAV operators don’t have to wait hours, or days, to understand what they’re seeing. Our Ground Control Station (GCS) streams live data straight from the drone to the operator’s screen, giving immediate insight into emissions behavior.
This live dashboard includes:
Methane concentration levels visualized as the drone flies.
Drone position and altitude for precise context.
Wind direction and speed from our on-site 3D ultrasonic anemometer.
Active maps and flight paths overlaid on satellite imagery.
Telemetry data like battery life and drone status for safe operations.
By combining environmental data, navigation details, and live methane concentration maps, the GCS empowers operators to make smarter decisions on the spot.
If a methane plume appears unexpectedly, the drone operators don’t just see it, they can adapt instantly, rerouting the drone to capture more detail, focusing on emission hotspots, or adjusting altitude to map the plume structure more completely.
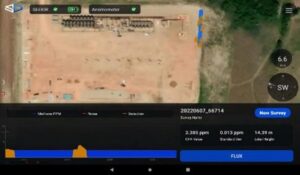
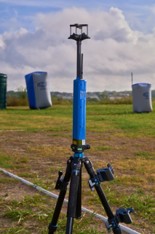
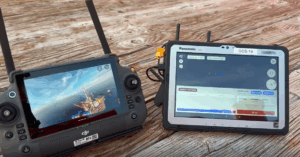
FASTR: Accelerating Results Beyond the Field
While GCS is all about awareness during the flight, the FASTR system, released mid-2025, addresses what happens after the flight. Traditionally, emissions monitoring relied on lengthy post-processing workflows, sometimes taking weeks before results were ready. FASTR shortens that cycle dramatically.
By automating the ingestion, processing, and reporting pipeline, FASTR delivers results in minutes, not days, without requiring any cellular connection. The platform organizes data from multiple flights, integrates environmental parameters, and produces clear emissions quantification reports that are easy to interpret and act upon.
For operators and asset managers, this speed translates into immediate value through rapid response to unexpected or large leaks, integration with mitigation workflows so that identified leaks can be prioritized, and quick validation of repairs, allowing teams to verify success before leaving the site.
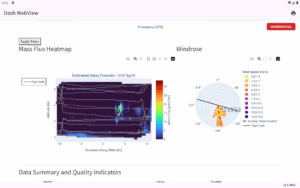
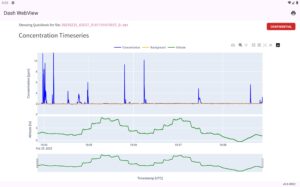
Why GCS + FASTR Matters
The real strength of SeekOps comes from combining the real-time situational awareness of GCS with the accelerated reporting power of FASTR. Together, they provide a seamless workflow from detection to action:
In the field: Drone operators see emissions data live, with the ability to investigate plumes before the drone even lands.
Post-flight: FASTR processes the mission data quickly, generating quick view quantification reports.
This dual system transforms emissions monitoring from a reactive process into a proactive management tool, enabling real-time awareness, rapid response, and quality assurance.
The Value of Speed and Certainty
In methane monitoring, speed is about more than convenience. Methane is over 80 times more potent than carbon dioxide in the short term, which means rapid detection and mitigation have a direct climate impact.
With GCS streaming and FASTR reporting, SeekOps helps clients move from data collection to climate action faster than ever before. Whether it’s an oilfield in Texas, a biogas plant in Europe, or an offshore platform in the Middle East, operators can trust that the data they’re seeing is accurate, timely, and actionable.
For industries under increasing regulatory pressure, from OGMP 2.0 requirements to the EU Methane Regulation, this combination provides both compliance support and operational efficiency.
Designed for Flexibility and Reliability
Both SeekOps apps are designed with field realities in mind:
Drone-agnostic integration means SeekOps sensors and software work with multiple airframes, from small quadcopters to long-endurance fixed-wing drones.
Lightweight payloads ensure minimal impact on flight performance.
Independent power systems maximize flight time without draining the drone’s batteries.
Built-in redundancy and QC checks reduce error margins and enhance reliability.
Whether operating in desert heat, offshore winds, or tropical humidity, SeekOps systems are tested to deliver dependable performance.
From Sky to Screen, From Data to Decisions
Methane monitoring has entered a new era. No longer do operators need to wait weeks for reports or rely on incomplete detection methods. With GCS providing live awareness and FASTR delivering accelerated results, SeekOps bridges the gap between measurement and mitigation.
Together, these tools give industries the power to act quickly, reduce emissions effectively, and meet the world’s growing demand for transparent, trustworthy climate data.
Stay tuned for the next post in our series: “Making Emissions Actionable – How SeekOps Reconciliation Reporting and Celsius Help Operators Close the Loop”
Ready to see FASTR in action?
Request a Live Demo today and discover how SeekOps helps you move from sky to screen—and from data to decisions—faster.
References
Corbett, A., & Smith, B. (2022). Study of a Miniature TDLAS System Onboard Two Unmanned Aircraft to Independently Quantify Methane Emissions from Oil and Gas Production Assets and Other Industrial Emitters. Atmosphere, 13(5), 804. https://doi.org/10.3390/atmos13050804
Dawson, K. W., Smith, B. J., Stocker, I., & Evans, P. (2024). Assessing the Application of Drone TDLAS Methane Emissions Monitoring Technology in the Intertropical Convergence Zone Using Machine Learning. APOGCE 2024. https://doi.org/10.2118/221317-MS
Smith, B. J., Buckingham, S., Touzel, D., et al. (2021). Development of Methods for Top-Down Methane Emission Measurements of Oil and Gas Facilities in an Offshore Environment Using a Miniature Methane Spectrometer and Long-Endurance UAS. SPE Annual Technical Conference and Exhibition, Dubai, UAE. https://doi.org/10.2118/206181-MS
Tavner, C. A., Touzel, D. F., & Smith, B. J. (2021). Application of Long-Endurance UAS for Top-Down Methane Emission Measurements of Oil and Gas Facilities in an Offshore Environment. SPE Offshore Europe Conference and Exhibition, Virtual. https://doi.org/10.2118/205467-MS
Ravikumar, A. P., Sreedhara, S., Wang, J., et al. (2019). Single-blind inter-comparison of methane detection technologies – results from the Stanford/EDF Mobile Monitoring Challenge. Elementa: Science of the Anthropocene, 7(1), 37. https://doi.org/10.1525/elementa.373
Gully-Santiago, M. A., Smith, B., Frederick, T., Dawson, K., & Elliott, D. (2025). Results and Learnings from the TADI 2024 Methane Quantification Trial. SPE Europe Energy Conference and Exhibition, Vienna, Austria. https://doi.org/10.2118/225634-MS